APPAREL OPERATIONS
Unlock your apparel business’s full potential with Technopak’s comprehensive operational consulting and strategic planning services
Apparel Operations
A Comprehensive Suite of Apparel Operations Consulting Services
Leveraging a rich heritage in Apparel Operations consulting services, Technopak empowers businesses to craft cost-effective strategies for the entire garment production process. Our top-notch apparel consulting & sourcing services ensure an end-to-end roadmap to optimise the value chain. With a keen focus on operational consulting, our apparel processing services aid you with target setting, cost estimates, stock optimisation, customer analytics and tools, and much more. Whether you’re an emerging or an established textile and apparel entity, leverage our deep expertise and transformation capabilities to foster sustainable growth and competitive advantage in the global market.
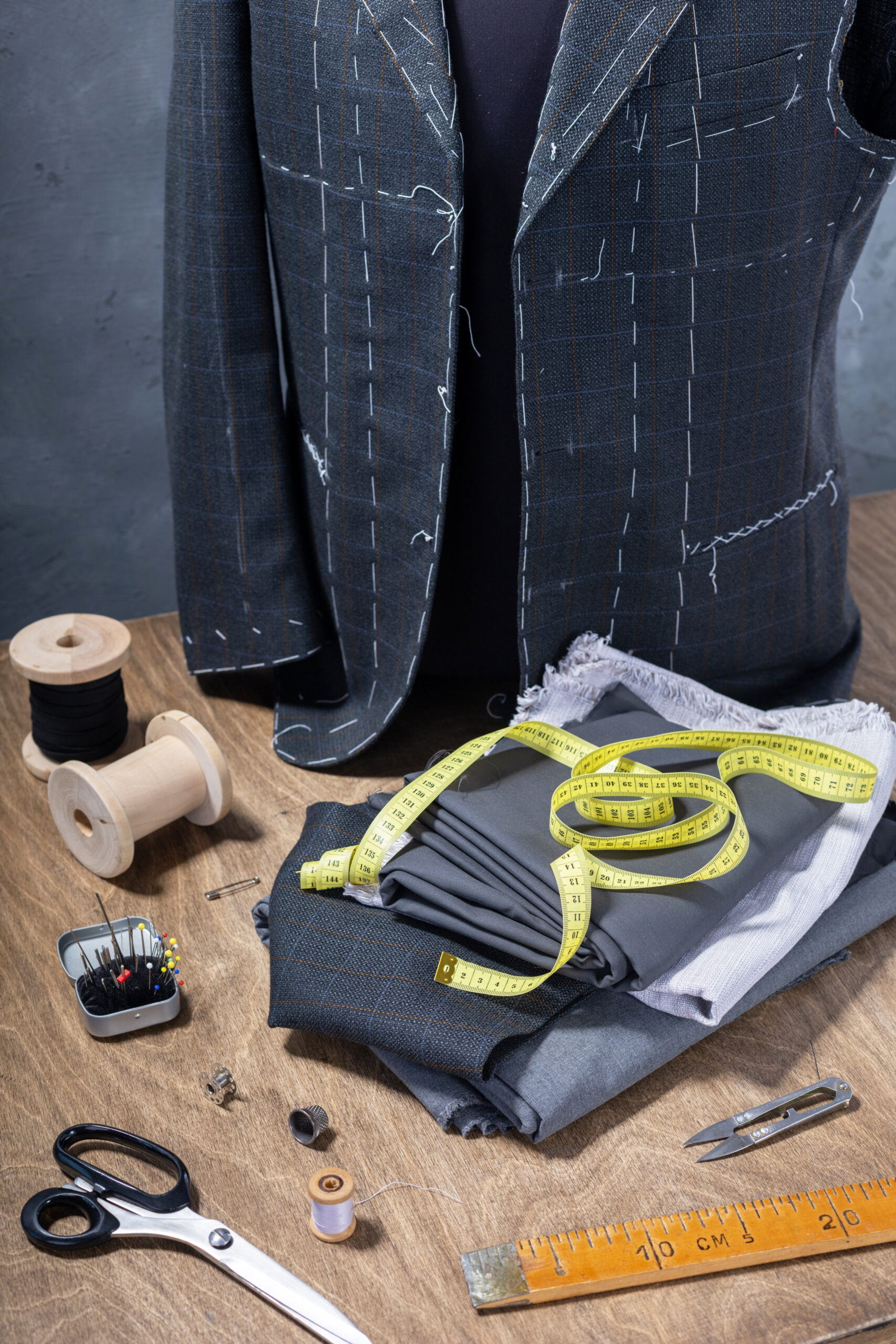
KEY SERVICE AREAS
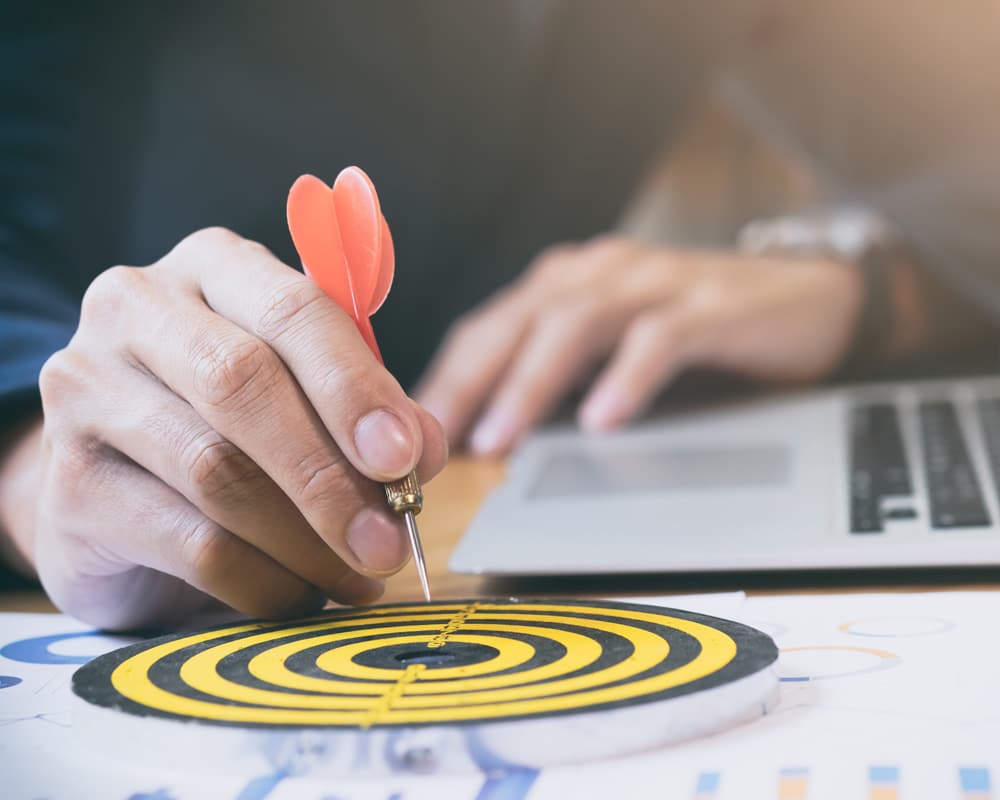
STRATEGY & PLANNING
- Business entry and growth strategy
- Business plan, resource requirement and key business numbers
- Manufacturing and supplying capabilities
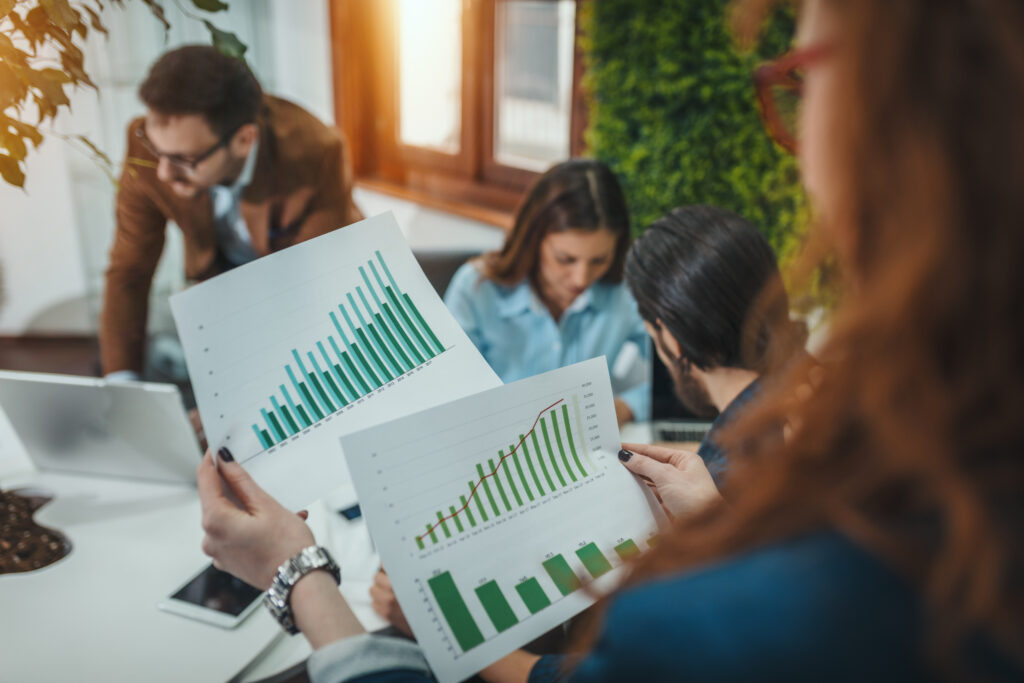
START-UP ASSISTANCE
- Planning and design of factory
- Implementation of layouts and processes
- Selection and training of middle management
- Efficiency and production build-up
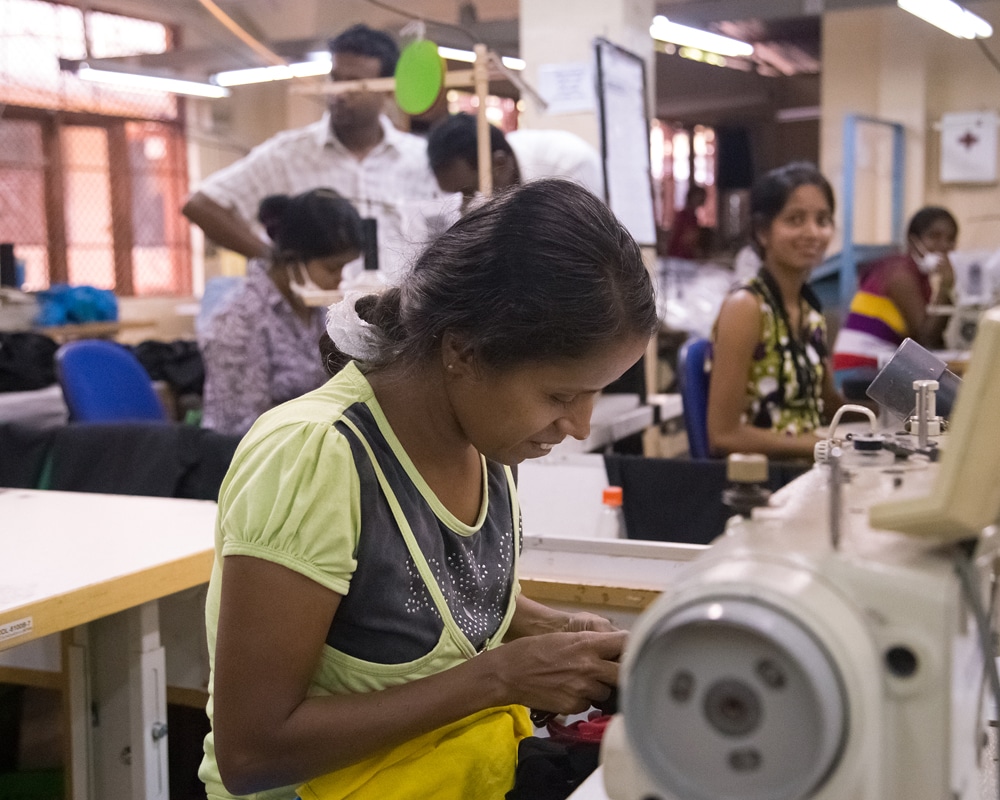
SETTING UP OPERATOR TRAINING CENTRE
- Program design and team profile development
- Setting up selection and recruitment criteria and procedures for operators
- Training operators on AAMT methodology
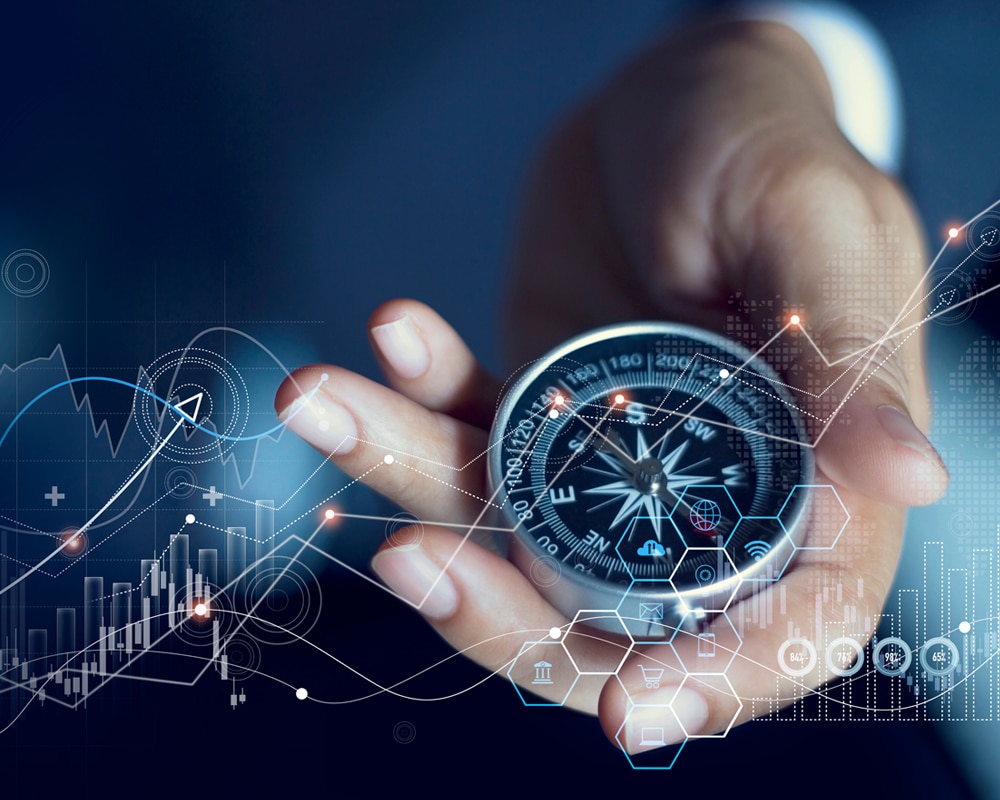
PERFORMANCE ENHANCEMENT
- Productivity/efficiency enhancement
- Material utilization and quality enhancement
- Streamlining merchandising and pre-production activities
- Lean manufacturing tools
- Visual control and SOPs
- Total quality management
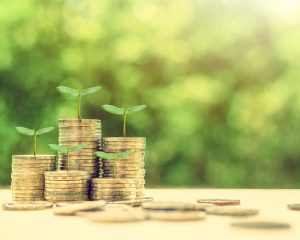
INCENTIVE SCHEMES
- Monitoring of individual operator performance and efficiency
- Designing performance-based incentive schemes for operators
- Development of KPI-based appraisal for middle management
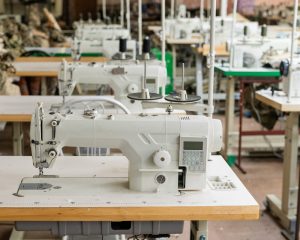
CAPACITY BUILDING
- Training need assessment
- Middle management training on master plato
- Training for merchandisers, quality personnel and industrial engineers
- Establish training methodology
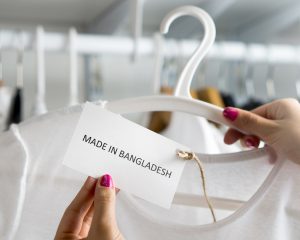
SOURCING SERVICES
- Industry landscape and product strategy
- Selection of key positions
- Identification, due diligence, training, and analysis of vendors
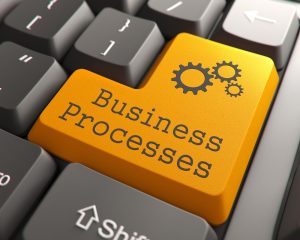
PRE-PRODUCTION STREAMING
- Capacity analysis
- Operator remunerations
- Setting time and method standards
- Layout and method improvements
- Production planning
CASE STUDIES
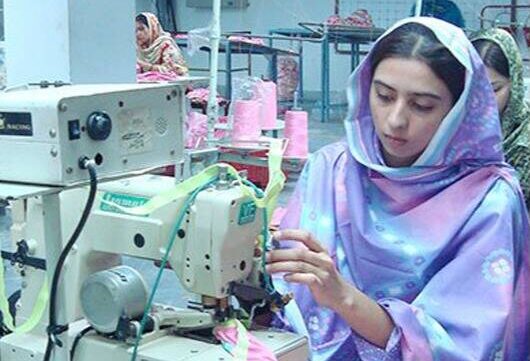
ASSISTING A GLOBAL DEVELOPMENT BODY IN EMPOWERING FEMALE GARMENTS WORKERS IN PAKISTAN
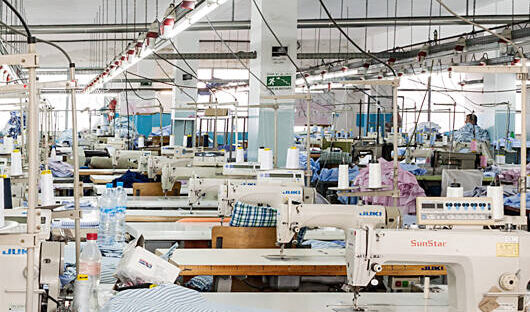
QUALITY IMPROVEMENT PROGRAM FOR A BANGALORE BASED MANUFACTURER-RETAILER
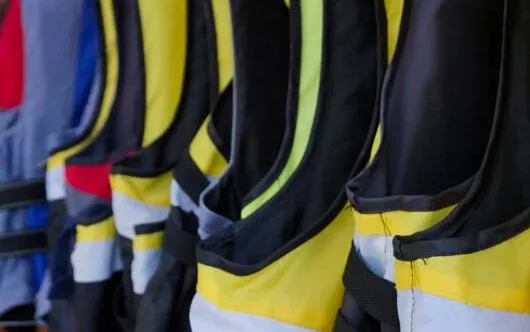
BUSINESS PROCESS RE-ENGINEERING OF A WORK WEAR MANUFACTURER-RETAILER IN BANGLADESH
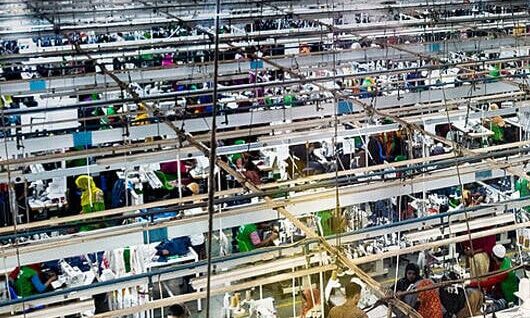
BUSINESS PROCESS RE-ENGINEERING OF A LARGE APPAREL MANUFACTURER BASED OUT OF BANGLADESH
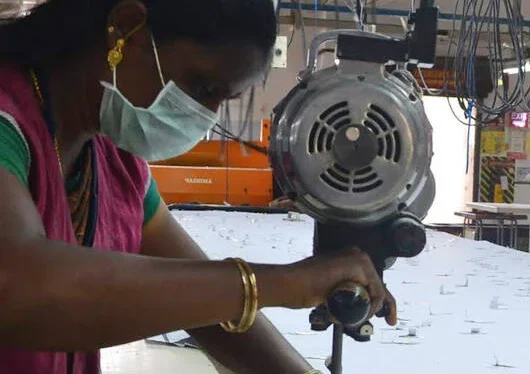